Interview with President Appears in “Paint and Coating Journal”
Dr.TAKUBO's COLUMN
An interview with Eiji Sasaki, President of TAKUBO Engineering, appeared in the March 22, 2006, issue of “Paint and Coating Journal,” a periodical focusing on the coating industry.
The article presents the views of President Sasaki on the development of environmentally compliant systems, based on TAKUBO’s own view of the coating industry in the near future. (Originally published in the March 22, 2006, issue of “Paint and Coating Journal.” Reprinted with permission of CoatingMedia.)
TAKUBO World, the Near Future of Coating?
Environmentally Compliant Systems Aimed at Changing People’s Thinking
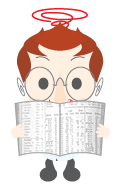
TAKUBO Engineering produces a line of coating systems that meet world standards. Our customers include manufacturers of data terminals for the IT field and producers of parts for car interiors. The number of our overseas clients is growing. Our products have been successful in an extremely competitive market because they meet two conditions that had previously seemed mutually contradictory: cost and quality. Now we are turning our focus to reduction of environmental impact. We are working in collaboration with producers of coating materials to create new coating systems for the near future.
— In April a revised version of the Air Pollution Control Act containing new VOC regulations went into effect. The degree of enthusiasm differs between companies, and it would seem that progress in this area is not going to be uniform.
“The environment is an important theme for manufacturing companies, including those in our industry. Environmental issues cover a broad range, including not just VOC reduction but cutting carbon dioxide emissions, reducing industrial waste, and dealing with toxic chemicals as well. The new VOC regulations are just one of the issues we are facing.
“The systems we offer are mostly used for applying plastic coatings, but in the world of small lots and many colors metallic coatings are becoming the norm. The quality requirements are very demanding, and the amount of cleaning solvent used when changing colors is much larger than the amount of actual coating material used. When it comes to two-component urethane coatings, not only is a lot of cleaning solvent used but an even larger amount of coating material ends up being discarded. We need to improve the coating adhesion rate, but we also will have to develop systems that eliminate the need for color changes if we want to really reduce VOC levels.
“Coating material producers are coming out with water-based coatings. These may help with VOC reduction, but they do not address the issues of carbon dioxide and industrial waste. We are working on a system that will reduce the amount of coating material used and also eliminate the cleaning process. This would be an approach to reducing environmental impact that would provide a total solution to the problem.”
— The drying oven also consumes a lot of energy.
“We think that we need to tackle the problem of reducing carbon dioxide emissions by focusing on two themes: creating more compact drying ovens and improving the heating efficiency.
“One special feature of metallic coatings is the need for a baking process. This consumes an enormous amount of energy. Few jobs only require one coat. Two coats require two baking cycles, and coating aluminum wheels involves three coats and three baking cycles. The undercoat contains a powder coating, but there is a base coat, a clearcoat, and then a solvent coating. This process hasn’t changed since the old days.
“There are drying methods that can achieve minimum energy consumption and achieve maximum effectiveness, based on the material of the work pieces being coated, the coating material, and the required quality. This year we want to make some new proposals, including this area. There are already efforts going on in South Korea to shorten and reduce the energy consumption of the drying process for two-component urethane coatings. We should be able to provide data and other reference information very soon.”
Aiming to Create Coating Systems Meeting World Standards
— In Japan there aren’t many equipment and machinery manufacturers or engineering companies that can offer total systems.
“This is something that is unfortunate both for the industry and for customers. In the past it was sufficient for equipment manufacturers and producers of coating materials to each offer products to customers on their own. But those days are long past.
“The production lines in the IT field, which we work with closely, are increasingly becoming clean room environments. Coating is also performed in a clean room. Comprehensive measures are taken to eliminate and prevent dust. The workers wear anti-dust clothing. Nevertheless, sometimes the coating materials contain foreign particles, so they have to be filtered before use. The gap that exists between the plants where the coating materials are produced and the plants where they are used is really amazing.
“In order to be able to offer total system solutions, we are going to have to become involved in managing the production of coating materials. We will have to form tie-ups only with partners that will allow us to perform such strict production management.
“I think it is very important for the coating material producer and the equipment manufacturer to work together as one from the standpoint of providing a superior product to the customer.”
— TAKUBO’s systems seem be building up an impressive track record overseas.
“Affiliates of the Samsung Group in South Korea occupy the central position, and the range of our customers also includes companies in China, Southeast Asia, and Brazil.
“The top manufacturers in each industry have expanded their operations worldwide, and they are working to achieve consistent quality throughout. At one time it was possible to select equipment and machinery individually each time a plant was built in a new location. Today there is a need to achieve consistent quality worldwide, so the trend is toward using the same coating systems at every plant.
“With regard to the environment, it is not acceptable to say don’t worry about it in this region because they have no regulations. The leading manufacturers adhere strictly to global standards that cover all of their operations. And they don’t hesitate when it comes to investment.”
Advanced Coating Systems—TAKUBO World
— Why are we now seeing strong sales of coating systems costing 100yen million or more?
“Probably because in the past there were no systems offering the quality and cost advantages we see today. Now it is possible to achieve both low cost and high quality in a manageable system. The items to be processed are subject to frequent variations in materials and coatings. In other words, there are many variables. At the worksite they are constantly studying these changes. Our data robot (DATASS-300) makes it possible to establish the coating method and conditions in a test chamber. This data can then be transferred coating robots in the work place so that coating can be performed under identical conditions.
“Furthermore, our “R-technology” coating method and the syringe pump, which can output minute quantities of coating material very precisely, make it possible to apply thin coating layers using a rotating system. The combination of this technology and the data robot cuts coating costs by about one-half. This is the basic concept. The key reason major customers have selected us is that we make it possible to determine precisely how much it costs per unit to coat a particular part.
“It is impossible to emerge successfully in international competition by relying on old ideas. It is necessary to satisfy the two conflicting goals of quality and cost. We must constantly keep introducing the latest technology. This also applies to environmental issues. We need to always take on new challenges, and this then becomes an issue of investment.”
— I have heard that at this year’s Paint Show you will be revealing your coating robots for the near future, with TAKUBO World as the key theme.
“We will be showing an animated presentation of our ideas on a big screen as well as SOFTBOY X, which will provide a hint of what is coming two or three years in the future. As for the ideas I just mentioned, we will propose a way to reduce coating material consumption and industrial waste by using a cartridge system for coating material. In this hose-less system the robot will be stationary and the work being coated will move. We want to reveal part of our efforts to reduce environmental impact through a total approach. We will also be showing the DATASS-300 data robot mentioned earlier and a new coating robot designed specifically for small work pieces.
“Environmental compliance is an important theme, but environmental issues are something that affect manufacturers and we can start to make changes today if we decide to do so. The real question is whether the will to act is there.”
Eiji Sasaki (TAKUBO Engineering)