Quick System(Compact UV coating System)
Not for sale under development
Reforming of coating system connected by conveyor line, that is, Conveyor-less Quick System.
From continuous transportation system to conveyor-less production system
In order to reduce the total energy (air conditioning, drying, distribution energy), it is indispensable to minimize the exhaust air volume of the booth, reduce the supply air volume, save the installation space, and have a high efficiency production style. "Quick system" (conceptual design) that integrates dust removal, coating, and drying booths centered on the Swan robot. The transport device with a rotation mechanism of the robot has realized the integration of painting equipment.
Think about the environment surrounding coating
Technology development by “TOSODO”
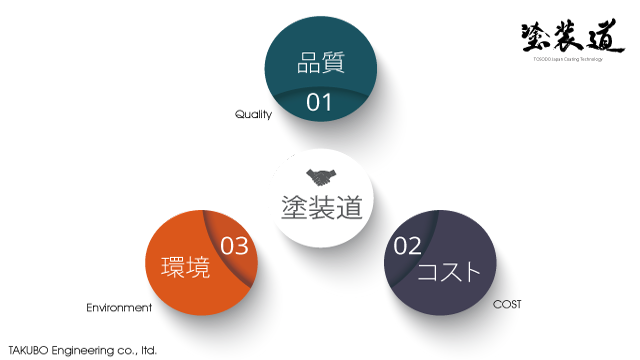
To the problems surrounding coating
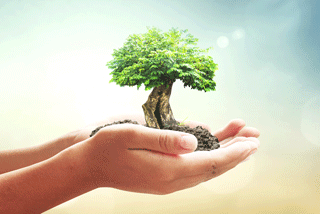
There are many problems surrounding coating such as carbon neutrality, realization of a decarbonized society, efforts to realize a sound material-cycle society, reduction of VOC emissions, working environment, cost competition, and competition for coating film products. When we think about what a coating system is ahead of the times as long as coating exists, it becomes a "quick system". Robotic coating technology called R technology has created a new coating system.
Selection criteria for coating system, summary of problems (requirements)
- Cost: Initial cost, cost-effectiveness
Cost control - Productivity: Mass productivity, high efficiency production system
- Cost: Running cost, total energy cost
- Quality: Stable coating film, stable production, quality that demonstrates the performance of paint
- Environmental measures: Reduction of wasteful energy, non-use of limited resources (water), reduction of VOC emissions, reduction of industrial waste (paint, sludge)
Coating system selection criteria, key to problem solving
- Specifications that can win the quality competition
Key to solve the problems - Specifications that can win the cost competition
- Environmental performance
Quick System
New coating system using UV paint
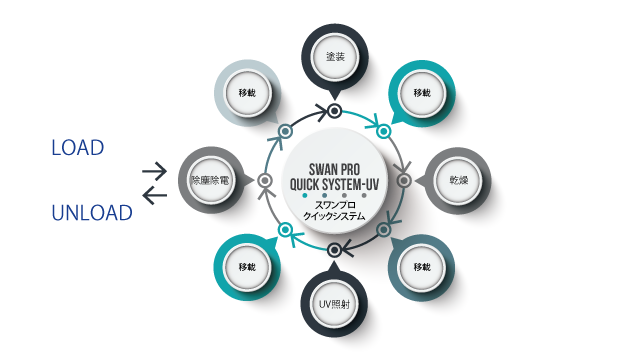
In a paint production system, modules in charge of painting, drying, etc. are generally placed on a conveyor line, which requires enormous space, production time, and energy. The newly developed "Quick System -UV" takes advantage of the characteristics of UV paint to form a coating film in a short time, and solves each problem in the form of a conveyor-less coating system. This is an epoch-making coating system that completes coating products within minutes from loading the work. We would like to propose a conveyor-less coating system along with UV coating.
Features
- Each module is made into a booth. Each process is arranged in all directions around the Swan Robot.
- It can be freely deployed from batch type to automatic system and line incorporation.
- Shortening coating production, downsizing installation space, reducing energy costs
- Supports multiple coats such as UV coating, 2 coats, 3 coats, etc.
Quick System means,
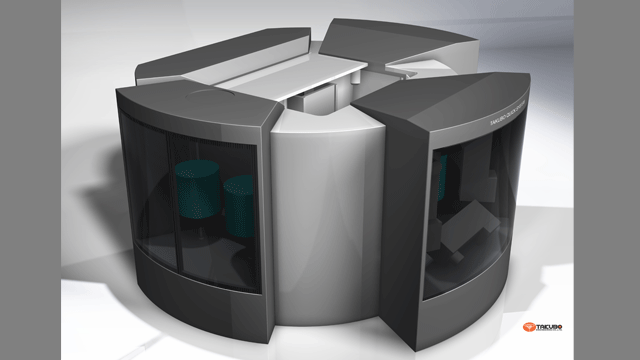
The quick system integrates the dust removal, coating, drying, and UV irradiation booth required for coating. It was developed as one package centered on Swan robots. We have eliminated the conveyor line and realized a conveyor-less system by using a handling device with a rotation mechanism of the Swan robot.
Purpose of development
How to reduce any loss in the coating system?
● What is a coating system that totally solves the problems of energy loss, paint loss, productivity and efficiency, industrial waste disposal amount, and cost generated when designing painting equipment on a conveyor line? "Quick system" was developed for the purpose of problem solving.
● One minute production is realized by coordinating a transport device with a rotation mechanism, a coating robot swan, and UV paint (ultraviolet curable paint), centered on a swan robot with R technology.
● How can it be produced in 1 minute? By reconstructing the coating system using UV paint, we will comprehensively solve problems such as energy loss, space loss, productivity, yield, and quality.
Normal coating line configuration
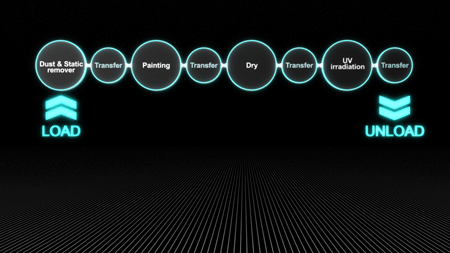
Usual line
Dust removal and static elimination → UV coating → solvent drying → UV irradiation → cooling drying → unloading
Normal coating line configuration centered on the conveyor line by connecting each coating equipment with a conveyor
Quick System coating configuration
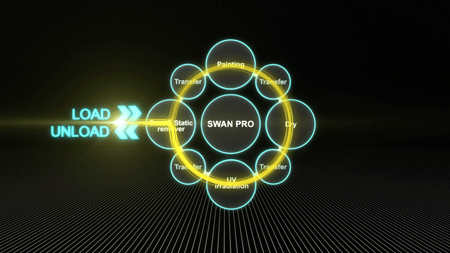
Quick System
Loading, dust removal, static elimination, UV coating, solvent drying, UV irradiation, cooling drying, unloading
Completed with one unit centered on the Swan robot
The transport device of the robot, centered on the swan robot, acts as a normal conveyor line and handles it. The conveyor line will not get dirty with paint, and no chain maintenance is required.
Centered on the SWAN robot
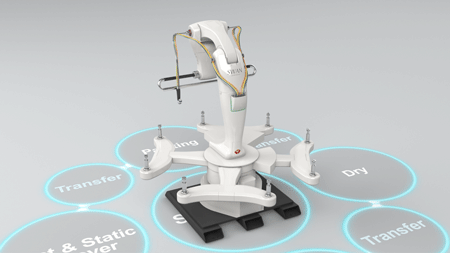
The work pieces are transferred to each booth by the swan robot placed in the center of the quick system and the transfer device of the robot.
Load
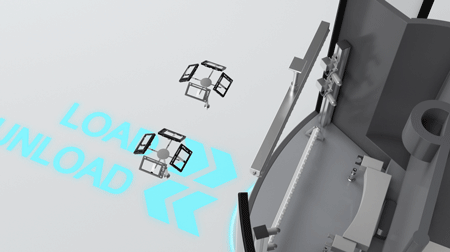
There are some loading methods: human intervention, using a handling robot, and using an AGV and a handling robot together.
Dust removal booth
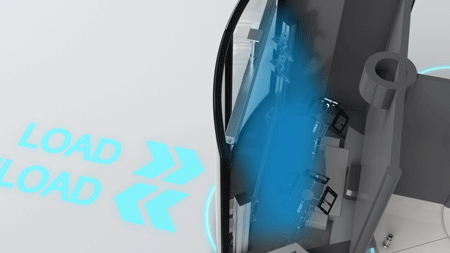
It is a booth that first removes dust and static electricity (disposal of dust) from the loaded work. Of course, the rotary partition (bulkhead) is designed so that it does not diffuse inside.
Coating booth
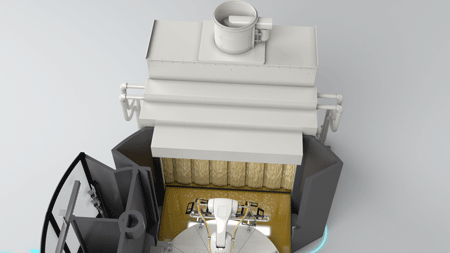
An oil booth is set up to collect overspray mist efficiently and quietly.
Coating by SWAN robot
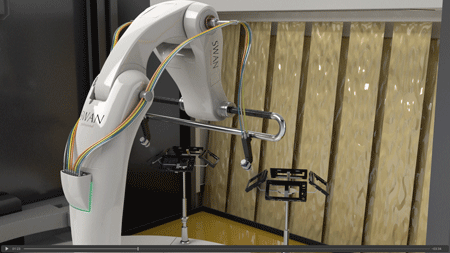
Swan robot makes a revolving coating using R-technology. . The multi-layer and thin film coating method reduces the use of unnecessary paint and enhances cost benefits.
Drying booth
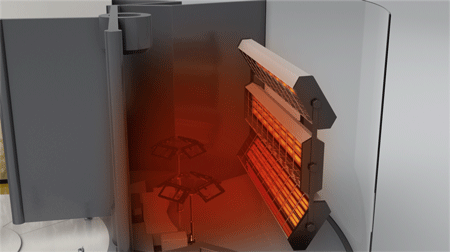
Designed as a solvent drying booth. The image of heating is based on the assumption of water-based paint.
Transportation
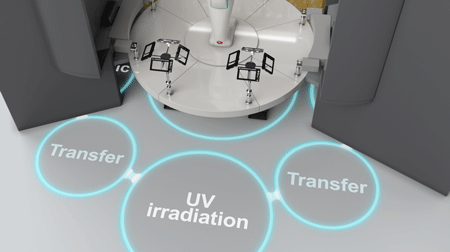
We make the best use of the transport mechanism of the Swan Robot to carry the transport between booths.
UV irradiation booth
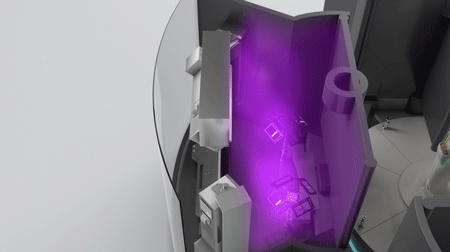
A booth for curing water-based UV curable paints.
We prevent leakage of UV irradiation in a shielded space, take safety measures, and efficiently irradiate UV to eliminate curing leakage. This is also handled by the rotation mechanism of the transport device of the Swan Robot.
The elements of R-technology are also utilized here.
Unload
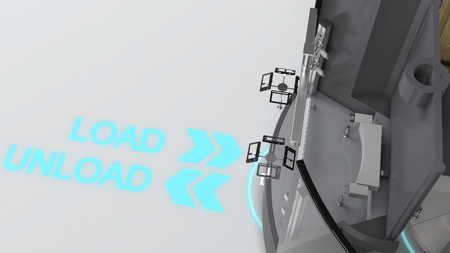
Although it passes through the dust removal and static elimination booth, it also uses air for cooling.
The entire Quick System
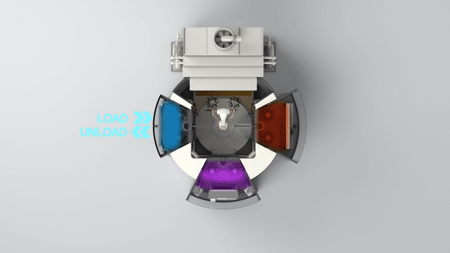
The Quick System, which eliminates the conveyor line and integrates the elements necessary for coating, makes the coating automation line extremely compact.
We will build a coating production system with a small installation space, effective use of limited factory space, and reduced coating costs.
Quick system Work attachment / detachment method and expansion examples
Attachment / Detachment method by human
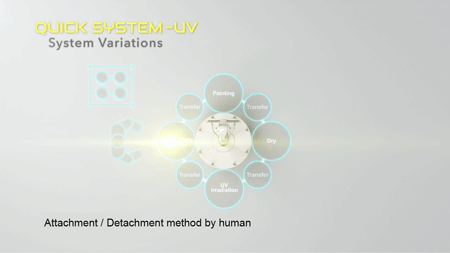
Attachment / Detachment method by handling robot
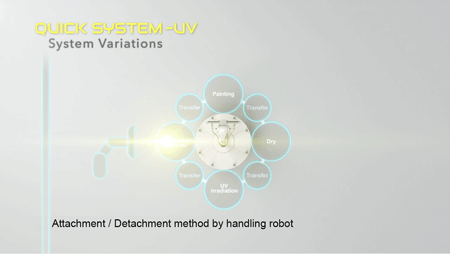
Quick System
Displayed at High-performance paint exhibition 2019
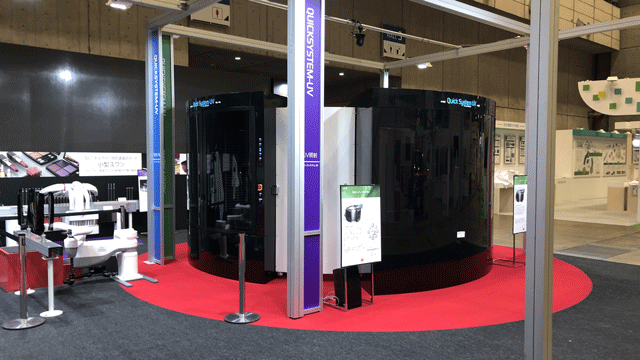
High-performance paint exhibition 2019 demo machine panoramic view
Dust removal and static elimination → coating → drying → UV irradiation → cooling is completed with this one unit.
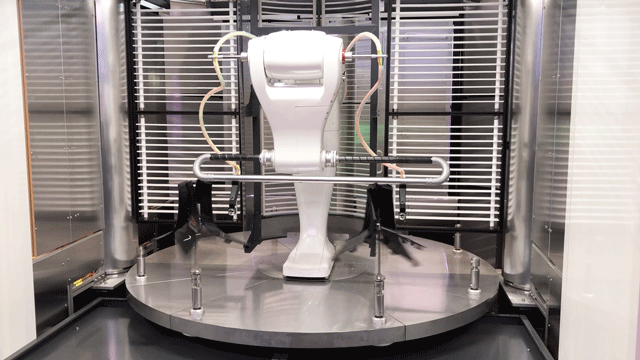
Demonstration machine Quick System internal photo for coating booth
Coating scenery of Swan Robot. The W-turn unit contains a transfer device.
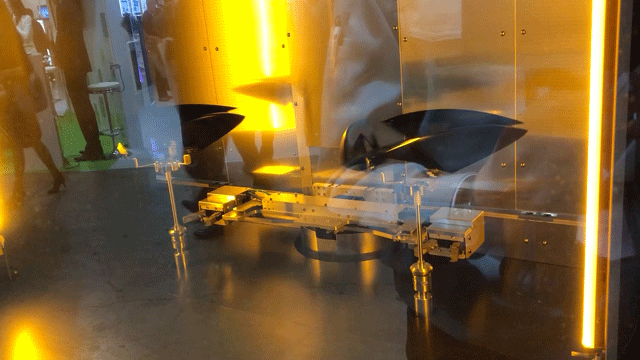
Taken from the outer circumference of the drying booth
The drying room is designed using the shutter (shielding plate) in the back of the photo.
Quick System UV
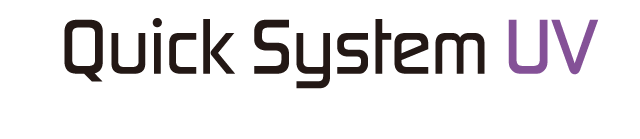
The quick system is a product under development.
- The quick system was exhibited and announced as a prototype at the 2019 High Performance Paint Exhibition.
- The quick system is a developed product and not for sale.
- Please contact us from this Takubo web inquiry page when considering.

2021年6月30日