Interview with President Appears in “Paint and Finishing News”
Dr.TAKUBO's COLUMN
An interview with Eiji Sasaki, President of TAKUBO Engineering, appeared in the April 5 issue of “Paint and Finishing News,” a periodical focusing on the coating industry.
What are we at TAKUBO aiming to achieve with regard to the theme of “future business expansion in the global age”? The article presents the views of President Sasaki. (Originally published in the April 5 issue of “Paint and Finishing News.” Reprinted with permission of Toryohochi Shimbunsya Co., Ltd.)
Ultimate Importance of Quality and Cost
Developments Utilizing Digital Technology
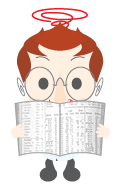
The coating industry is constantly confronting environmental issues. This is true throughout the world, and it goes without saying that when we install a new system in a country we must conform to that country’s standards. But it goes further than this. We must supply systems that match the corporate stance of the countries in which we wish to do business. Environmental issues are global in scale. It is not enough to focus only on legal standards. The important thing is the corporate philosophy.
One thing we must consider is what we want the coating industry to become in ten years’ time.
Environmental considerations will become even more strict, and at the same time we must deal with quality and cost as the most important issues.
The mobile devices and automobile parts industry, which is where we are active, deals with work pieces that are small in size but extremely large in quantity. The volume of coating material consumed is enormous. In addition, the plants where this coating is performed are scattered all over the world. The specific environmental problems in each country differ, but it is important for us to view the environment as a common issue that is global in scale and to overcome it.
One issue that we have to address in Japan has to do with water-based coating materials. With the revision of the Air Pollution Control Act, there has been a partial shift from solvent-based to water-based coating materials. This has given rise to some difficult problems for companies in the coating field. The coating material producers feel that they must give their products an environmentally friendly image. In fact, even with the shift from solvent-based to water-based coating materials, the amount of solvents used is not decreasing; it is increasing. The reason is that though there is now less solvent contained in the coating materials, more solvent is being used for cleaning.
Most of today’s water-based plastic coating materials can be cleaned up without using acetone alcohol.
The recent trend is toward increased production volume, but the number of pieces per lot is decreasing. This means that frequent color changes must be performed. Against this background the industry is demanding improvements in both coating systems and coating materials.
There are a number of technical hurdles that we must overcome during the next decade. It has been nearly 20 years since TAKUBO started introducing ceiling-mounted robots. Recently, we have developed “R-technology” employing multiple guns (up to eight guns at once). We are proceeding with our business activities with this coating method in the central position.
In the past, the robot held a coating gun and moved in the way a person would to perform coating. We realized that this was not a suitable way to coat small work pieces (such as mobile phones, digital cameras, personal computers, and automobile parts) and determined that the best method was to rotate the work and have the coating robot wait for the work to come round to it. We call this coating method “R-technology.”
Our coating method results in a substantial reduction in the amount of coating material used, compared with conventional methods. It also shortens the time required for coating. Thus, it clearly provides advantages in terms of both quality and cost. I think it is also an effective way of meeting the requirements of VOC regulations.
At present the maximum number of guns per robot is eight. Mobile phone parts can be coated at a rate of 0.5 seconds per piece. When coating at this kind of speed, a single gram per work piece adds up to an enormous amount.
In an industry like mobile phones, in which a single company produces hundreds of millions of units, a coating material volume of one gram per work piece works out to several tons total.
Very important issues in developing the coating systems of the future will be reducing consumption of coating material and energy to the minimum possible while attaining the best quality and cost. It will be necessary to develop a number of new technologies to achieve these aims.
One is digitization of the coating process. If you look at Japan’s coating plants, you’ll see a lot of analog systems. Analog coating methods are not bad, but they have serious problems when it comes to dealing with today’s product development demands—speed, quality, cost—as well as the difficulty to training enough technicians to operate them.
It is particularly difficult to train technicians overseas. Among our customers, there is much more demand for digital systems overseas than there is here in Japan. We have developed the DATASS-300 system to meet this demand.
This system does not require use of the production line to generate coating data. A separate, dedicated data generating robot (DATA PRO) is used for this purpose. The data is then transferred to the production line.
Another feature of DATA PRO is that it is a data generation system that lets you achieve the best results in terms of cost and quality. It allows you to check the coating cost—the amount of coating material used and the coating time—immediately after coating finishes. Employees can send optimal data to plants anywhere in the world, whether in Japan or overseas. This is an exciting feature of digitization.
Companies that have introduced this system have found that a person with no experience at all in the coating field can achieve extremely high-level results after just three months. They are amazed. Today’s young people have difficulty learning how to use analog systems, which require years of training and practice to master. But they can learn the ins and outs of a digital system quickly and easily.
DATA PRO is gaining popularity among coating material producers, both in Japan and overseas. Some companies require color samples with good reproducibility, and the digitization of coating processes proceeds.
TAKUBO is continues development work aimed at further digitization. But there are many problems that equipment manufacturers like us cannot solve on our own. There is an urgent need for coating material producers, coating equipment makers, and manufacturers who use coating systems to work together on the development of new systems.
In the near future TAKUBO plans to introduce a new system that will help solve problems in the areas of coating material performance, VOC emissions, and industrial waste.
We’re not too concerned about what methods have been used in the past. We think that any method that makes it feasible to manufacture products with the minimum energy consumption possible is good. No matter how excellent the coating results, if the costs are too high you will be left behind by the times. That is a fact. This is why I think that shifting quickly to numeric control and digitization is a key theme.
Eiji Sasaki (Tokyo, President of TAKUBO Engineering)