Rotation jig for outside mirror coating(Outside mirror coating system)
R-technology includes the design of rotation jigs
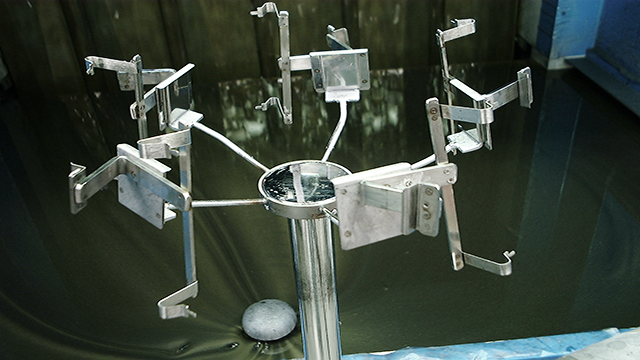
The design of rotation jigs, which is important for the revolving coating, will have a significant impact on the coating film performance, the coating cost and the coating quality. Even the work fixing position or the inclination degree is a big influence factor. The design of rotation jigs is an important technology in the revolving coating “R-technology”.
Placing the work pieces to avoid a waste movement of the robot
Base part of outside mirror
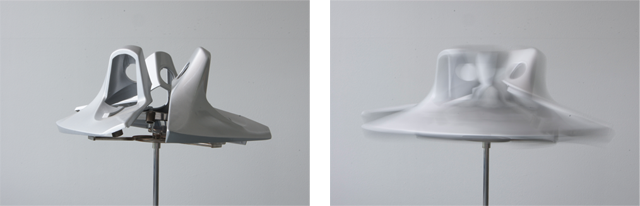
Base part of outside mirror
The above picture is an example of base part of outside mirror placed on a rotation jig. Setting up the workpieces within the circle range of about 500mm diameter, and placing the face necessary to coat towards the outer circumference. And then imaging movement of the robot on the revolving workpieces. The best work placing position is determined when you see a very simple orbit line of the robot. Receiving jig is designed according to the best placing position.
Cover part of outside mirror
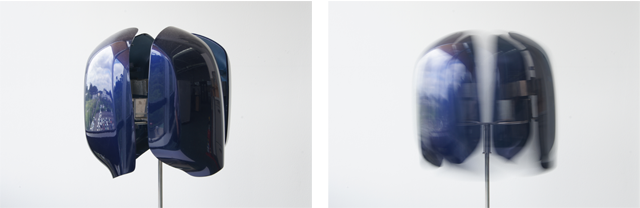
Cover part of outside mirror
The above picture is an example of cover part of outside mirror placed on a rotation jig. Imaging revolution of this workpieces, a relatively simple cylindrical figure comes out. Teaching the robot along the outer circumference realize a multi-layer and thin-film coating in a short time without any waste movement of the robot. Considering size and shape of the workpiece, the number of the work piece to mount on a jig is determined.
Imaging the robot movement
Robot movement and spray conditions
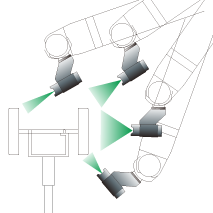
Waste movement of the robot will have a big impact on the coating time. Revolving workpiece look like a cylinder or cone. The outer circumference becomes a surface. Robot teaching should be done towards the outer circumference without any waste movement. Being different from conventional net coating or teaching of coating for fixed workpieces, our method is to spray turning (heading) workpieces so that the robot teaching is very simple and easy (DISK PACK, KEITAI PACK).
Design of receiving jig
Examples of jig design for outside mirror parts

Factors to consider in jig design
- Jig design for outside mirror parts coating is determined considering various kinds of factors such as workpiece fixing positions, vertical or horizontal placing, and coating time.
- Production volume, robot movement, film thickness, sagging and lack of hiding
Handling of workpieces
Jig considering removal
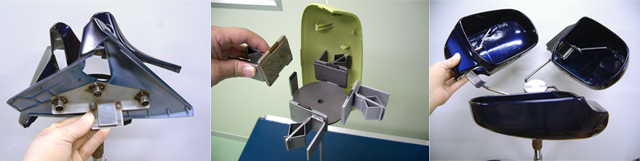
Considering ease of installation of workpiece
In case of the revolving coating, it is very important to fix the workpieces so firmly on the jig that the workpieces never be removed in coating. During installation and removal, however, a bad workability will bring a bad influence on the coating quality or the productivity.
Type of jig
Examples of jig design by work shape or conditions
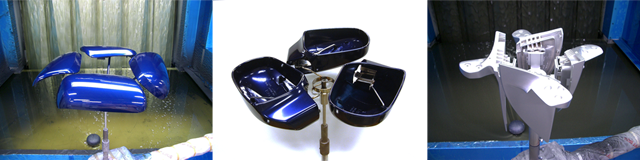
There are basically two types of the jigs for outside mirror, i.e. horizontal placing and vertical placing. Considering the paint performance, required quality including necessary film-thickness, production volume per hour and coating time etc., one of them is chosen so that the robot has no waste (surplus) in its movement.
(Left) Horizontal placing rotation jig with 4 pieces.
Without any waste of the robot movement, the multi-layer and thin-film thickness coating is realized. (Outside mirror cover)
(Middle) Horizontal placing and face-down rotation jig with 3 pieces.
Jig example to coat especially edge or inside parts of outside mirrors (Outside mirror body).
(Right) Vertical placing rotation jig with 3 pieces.
Coating whole base parts of outside mirror in details (Base part of outside mirror)
Points to consider in jig design
Coating cost changes substantially depending on the jig design. Considering some important factors, the jig design should be determined including placement with the workpiece inclination.
Coating time and production volume
Grasping how many workpieces to load on a jig
Area to coat and robot movement
Imaging the areas to coat and not coat, or the sagging area or the area of lack of hiding.
Installation, removal and handling
Considering the way to avoid any shift and removal during revolving coating or transferring by handling robot, and also the way easy to remove the workpieces in unloading or inspection.
Jig size
The circle diameter of the jig with workpieces should be less than about 500mm in designing.
Robot movement
Imaging no waste movement of the robot in the jig rotation.
Trying not to make any cause of dust defect.
Considering the structure in which floating dust or over-spray mist never adhere.
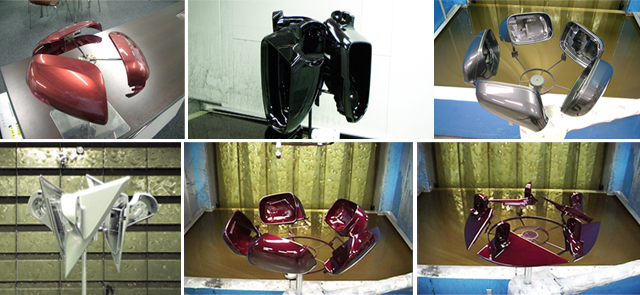
Considering production volume, film thickness, handling and so on in jig design
Release date: July 21, 2017