Pursuit of revolving coating(by fluid simulation)
Author: Hikaru Kojima, Senior Manager of Technology Development Division
60th Anniversary Issue of Coating Technology Published in July
What we have learned by using fluid simulation technology
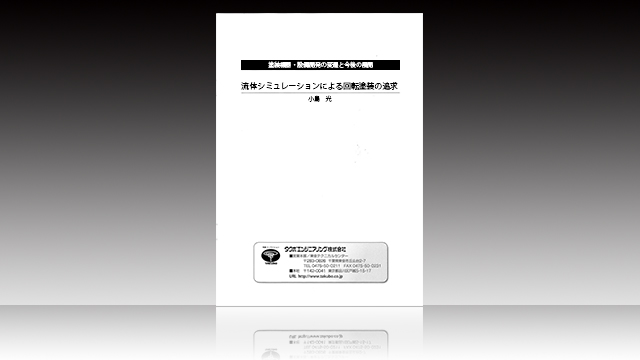
We would like to introduce what we have learned by utilizing fluid simulation technology for "revolving coating by R-Technology" and general coating method "net coating" and "spindle coating".
Pursuit of revolving coating by fluid simulation
We pursue "revolving coating by R-Technology" that achieves both high productivity and high quality with a small amount of paint, and provide many coating robot systems that utilize the advanced technology.
R-Technology means: A general technology term of Takubo Engineering Co., Ltd. that we have been pursuing revolving coating for many years. In addition to turning and applying, it has various mechanisms that can "pursue the limit" of the amount of paint used.
Currently, we are developing "SWANIST", a teaching assist software that gradually transforms toward DX (digital transformation) of coating. This evolved software actively utilizes fluid simulation and artificial intelligence (AI) to thoroughly analyze and eliminate paint and work waste.
In this content, we would like to introduce what we have realized by visualizing and quantifying "revolving coating by R-Technology" and general coating method "net coating" and "spindle coating" proposed by our company using fluid simulation technology.
1. What you can see when you use fluid simulation technology for coating?
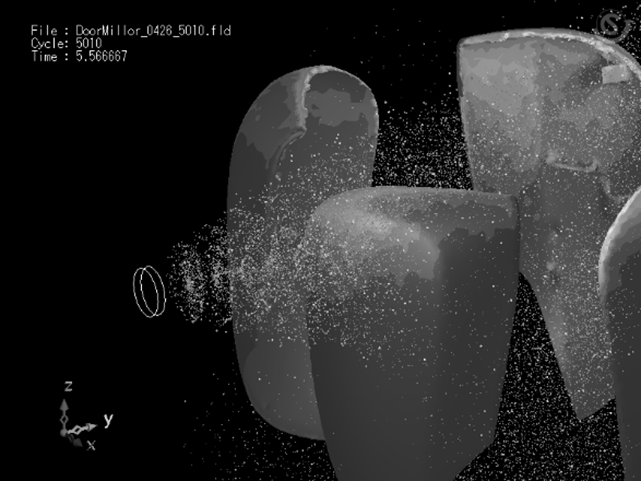
Since the coating simulation calculates and tracks each particle ejected from the spray gun based on the equation of motion, observe and analyze how the spray particles are affected by the air flow and fly. Moreover, since the number of particles ejected and the number of particles coated on the workpiece can be counted, the amount of paint discarded can be easily calculated. (Calculation of coating efficiency and amount of paint used)
2. What we have learned by simulating coating
The targets of the simulation were the "revolving coating method using R-Technology" proposed by our company, the general coating methods of "net coating method" and the "spindle coating method". As the analysis conditions, realistic conditions are set as much as possible.
The results of simulation comparison of the three types of coating methods are below.
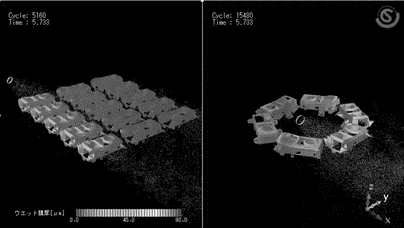
① Comparison result of coating efficiency of "net coating" and "revolving coating by R-Technology" ※The same workpieces were compared by placed on a net or ring.
- Coating efficiency of net coating : 【19.3%】
- Coating efficiency of revolving coating by R-Technology : 【45.3%】
②Comparison result of coating efficiency of "spindle coating" and "revolving coating by R-Technology"
- Coating efficiency of spindle coating :【7%】
- Coating efficiency of revolving coating by R-Technology :【42.3%】
- ※Revolving coating by R-Technology assumes SWAN-C that follows the conveyor as shown on the right in illustration 3.
※ Details of the new robot "SWAN-C" will be omitted. (Please check the November 2020 special issue)
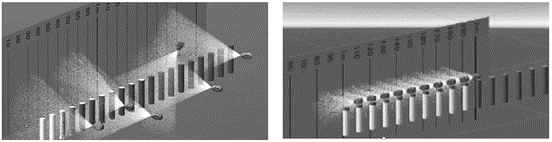
From the analysis results of ① and ②, it was found that the coating efficiency of "revolving coating by R-Technology" is about twice of "net coating" and about 6 times of "spindle coating". It was proved that "revolving coating by R-Technology " is a method with much better coating efficiency.
3. The reason why the coating efficiency of revolving coating by R technology is much better (Comparison with net coating)
In fluid analysis, it is possible not only to calculate the coating efficiency and the amount of paint used, but also to divide the phenomenon in time and analyze it in detail. Spindle coating is a partial coating through which the work passes and is not a comparison target, so it will be omitted here, and comparison with net coating will be used.
<Reason 1>
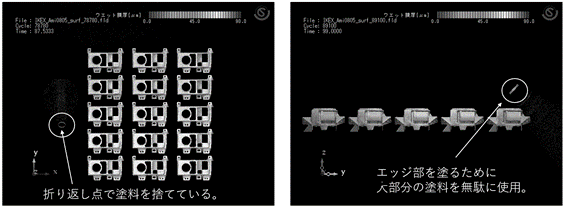
In principle, the paint is always discarded at the left and right folding points in the net coating. Also, as shown in illustration 4, most of the paint is wasted just to coat the edges.
<Reason 2>
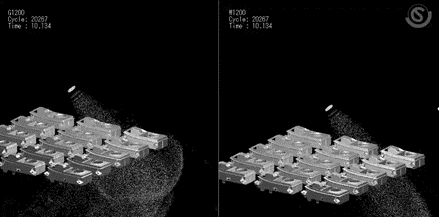
In net coating, because the spray gun moves at high speed, the paint is difficult to apply. Since it is necessary to compare under the same conditions to prove this, we analyzed the case where the spray gun moves and the case where the workpiece moves.
As shown in Illustration 5, the mist is diffused because the spray gun moves at high speed in the net coating. When the mist spreads, the probability of applying to the workpiece will decrease, that makes the paint difficult to apply. On the other hand, when the workpiece moves, the mist is stable even though the workpiece is moving. When the mist is stable, the probability of coating on the workpiece will increase, so the coating efficiency also increases.
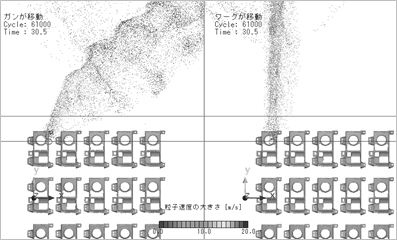
Illustration 6 shows the spread of mist in an easy-to-understand illustration. In the left picture, if the spray gun moves at high speed (net coating), the mist is diffused and the speed of the particles is slowing down. When the spray gun moves, the mist hits the stopped air and diffuses and slows down. If the speed of movement of the spray gun is further increased, the tendency becomes more remarkable and more difficult to apply.
On the other hand, in the right picture, when the workpiece moves at high speed (revolving coating by R-Technology), the spray gun moves slowly, so the mist is stable and the particle velocity is maintained, so the coating efficiency is improved.
<Reason 3>
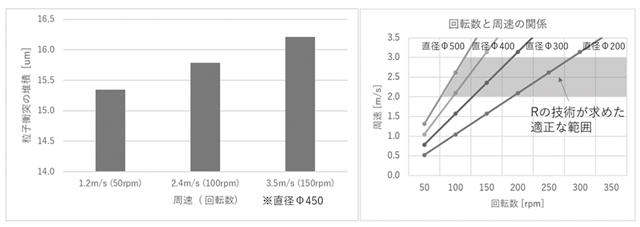
In revolving coating by R-Technology, the optimum peripheral speed is required for each workpiece diameter. (Graph on the right in Illustration 7) By doing this, even a small amount of mist passing between the workpieces are picked up and attached to the workpieces. In the left graph of Illustration 7, the vertical axis is the coating film thickness and the horizontal axis is the peripheral speed, but the coating efficiency is improved by the optimum peripheral speed. The appropriate revolving speed for each workpiece is calculated from this peripheral speed.
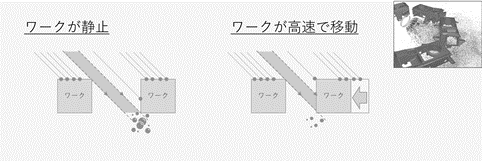
Illustration 8 is an illustration of the case where the workpiece is stationary and the case where the work is moving at high speed. When the workpiece is stationary (net coating), the mist passes through the gap between the workpieces and a certain percentage of paint is wasted, but when the work is moving at high speed (revolving coating by R-Technology), the gap particles that should pass through can also be picked up and attached to the workpiece. Therefore, overspray between workpieces can be reduced.
The reasons why the coating efficiency of "revolving coating by R-Technology" is much better are summarized below.
- Reason 1 Since there are no left and right folding back points, there is less overspray.
- Reason 2 There is no disturbance of mist and it is stable.
- Reason 3 The amount of mist that passes between the workpieces is reduced.
4. The reason why the productivity of revolving coating by R-Technology is higher (comparison with net coating / spindle coating)
In principle, the only way to increases the number of productions by net coating is to increase the moving speed of the spray gun and increase the discharge rate. It will change the coating conditions and difficult to balance a quality. Also, since there is a lot of overspray due to folding back points, the higher the number of productions, paint will be thrown away.
Next, when increasing the number of productions by spindle coating, there is no other way but to "increase the conveyor speed" in principle. In addition, as the conveyor speed increases, the coating efficiency will be decreased, so it becomes necessary to "increase the number of fixed spray guns and increase the discharge rate."
In the spindle coating simulation, it was confirmed that the coating efficiency decreased in proportion to the conveyor speed, and it was also confirmed that it was necessary to increase the number of spray guns and the discharge amount in proportion to the conveyor speed. (Table 1)
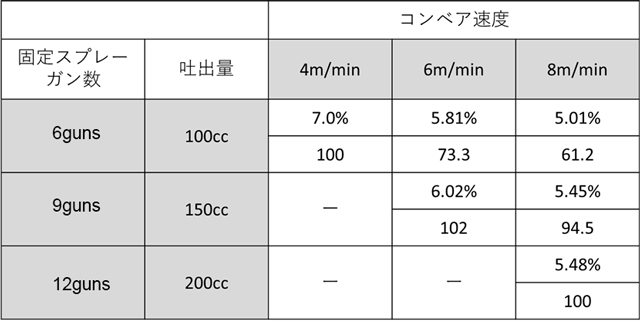
※The upper part of Table 1 is "coating efficiency" and the lower part is "coating film thickness coefficient".
※"Coating film thickness coefficient" is the relative coating film thickness with coating the film thickness at the conveyor speed of 4 m / min in the upper left of Table 1 as 100.
On the other hand, in the revolving coating by R-Technology, it is possible to increase the production number by coating multiple rings at the same time. (Illustration 9)
- Spray guns without variation are installed as a condition for coating multiple rings without variation.
- It is equipped with a syringe pump that can discharge a fixed amount. This makes it possible to increase the number of production while maintaining the quality without changing the coating conditions.
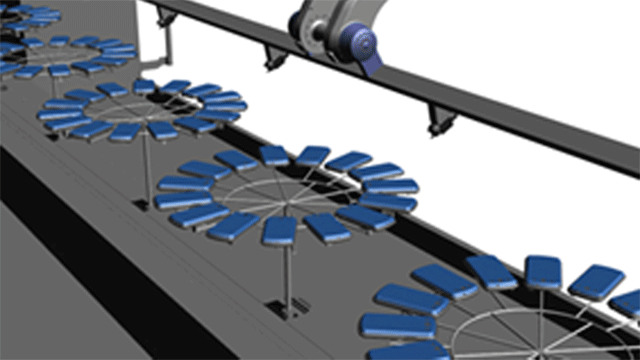
5. Conclusion
The environment surrounding coating is changing day by day, and in recent years it has become essential to respond to the environment issues in particular. In the coming era, paints and equipment will be required to change according to the times.
Analysis revealed that the conventional coating method in which the robot chases the object to be coated is inefficient in principle regardless of whether it is a small work or a large work, and there is a lot of waste of paint. On the other hand, it was proved that "revolving coating by R-Technology", in which the spray gun moves slowly and the object to be coated revolves, has less waste of paint in principle.
We will continue to make full use of the latest technology to develop coating systems that respond to changes in the times and the environment, and hope to contribute to solving social issues.
60th Anniversary Issue of Coating Technology Published in July
Hikaru Kojima, Senior Manager of Technology Development Division
Issue date: 30th July, 2021