High grade coating technology, R-technology(Outside mirror coating system)
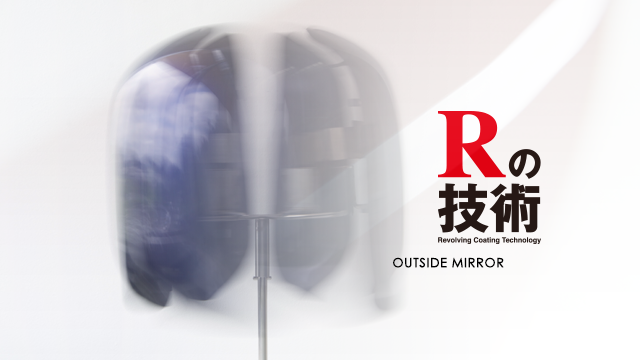
High grade coating technology
The high grade coating technology, “R-technology, forms the ultimate controlled thin film.
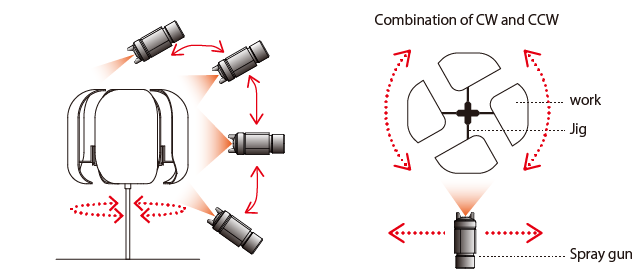
High grade control combination
Robot movement, workpiece revolving control, and spray gun control with gun distance. High grade combination of those can realize the thin-film and multi-layer coating. It satisfies the requirement about quality, cost, and some theme of environment.
Control of spray gun is to control the film thickness.
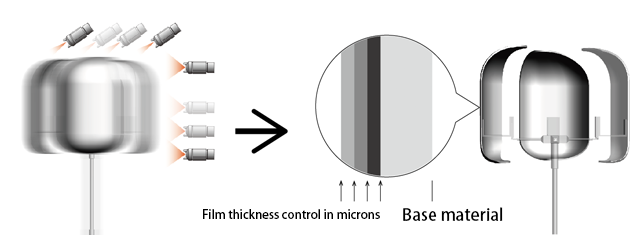
It is possible to intuitively change spray conditions depending on the gun's aiming place.
The number of spray-pass in the revolving coating is overwhelmingly more than that in the net coating. Coating thinly and repeatedly can draw texture of the paint to maximize especially in metallic and pearl coating. In case of complicated shape workpieces, it should be thinly and repeatedly coated in changing gun’s aiming points. Because the rotation number of the workpieces becomes the number of spray-pass in case of the revolving coating, the pass number is overwhelmingly more than that of the net coating so that “R-technology” can realize the excellent multi-layer and thin-film coating which the net coating or the hand spraying never produce. Furthermore, it is able to form the high grade coating film by changing the spray conditions depending on the gun’s aiming position.
Robot teaching without waste movement

Substantial reduction of the paint consumption volume
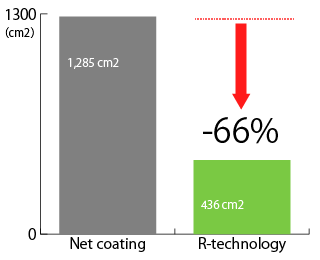
The revolving coating “R-technology” can reduce the paint consumption volume very much so that it is almost 1/2 through 1/3 compared to those of the net coating and spindle coating. One of the reason is that the over-spray region (area) of the revolving coating is much less than those of the net coating and the one-piece spindle coating, that is, about 1/3 and about 1/8 relatively. That is why the paint consumption volume can be substantially reduced in “R-technology”. Furthermore, our original peripheral devices, the spray gun “SUKOTTI GUN” with excellent atomization at low pressure and also the syringe pump with high precious control in 1 cc unit can contribute to substantial reduction of the coating cost in control of all the equipment by the robot.
- The revolving coating “R-technology” with multi-layer and thin-film coating
- SUKOTTI GUN with fine atomization at low pressure
- Easy teaching
- Compatible teaching data
- Syringe pump possible to control precisely in 1 cc unit
Easy condition setting and visualization of coating
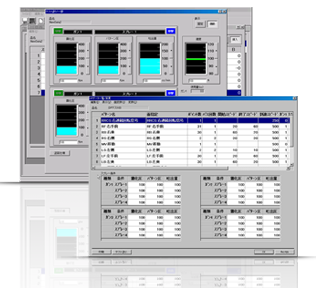
Standard equipment FA PC can make it possible to input parameters for discharge volume, atomizing and pattern of each spray gun. And the revolving coating is not necessary to make complicated teaching work. It is a very easy operation just to trace the revolving body.
- Easy editing operation by the original teaching software
- Management of the data such as spray condition setting and teaching data is possible.
- High grade data compatibility with other robots of TAKUBO
Importance of jig
Important role for productivity
The reason why the jig design plays an important role for productivity is based on the robot movement and the reduction of paint consumption. They are the most important parts to make a stable quality, increase the production efficiency, and manage the coating cost.
Work position to finish thinly and quickly
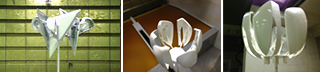
Control of revolving workpieces and very simple movement of robot, which are supported by the jig design. The most appropriate position of the work pieces embodies multi-layer and thin-film coating and also realizes the high grade coating film.
Rotation jigs are developed in consideration of various conditions
- Coating area of workpiece
Installation and removal of workpieces - Minimal movement of the robot
- Easy position to coat for the robot
- Work placing to be in the cylinder zone of aboutφ450 toφ500mm
- Easy workability to install and remove workpieces on/from jig or masking jig
- Dirt resistant by over-spraying
Options / Related Products
Release date: July 21, 2017